Implementación del método Lean Manufacturing
Lean Manufacturing es una filosofía de gestión que busca maximizar el valor para el cliente eliminando los desperdicios. La clave de Lean está en mejorar continuamente los procesos, para que cada recurso invertido en la producción, desde el tiempo y los materiales hasta el esfuerzo humano, se utilice de la manera más eficiente posible.
Desde el mes de junio, hemos iniciado un ambicioso proyecto de mejora continua en nuestra empresa, basado en la metodología Lean Manufacturing, específicamente en la implementación de las 5S. Esta metodología, ha demostrado ser altamente efectiva en diversas industrias, optimizando la eficiencia, mejorando la calidad y reduciendo costes. Nuestra meta es crear un entorno de trabajo más ordenado, seguro y eficiente, que al mismo tiempo favorezca el bienestar de los trabajadores.
¿De dónde procede esta nueva forma de trabajo?
Esta forma de gestión presenta su origen en Japón en la década de 1960 por Toyota, con el propósito de crear entornos laborales más limpios, organizados y eficientes.
Tras la Segunda Guerra Mundial, la Unión Japonesa de Científicos e Ingenieros impulsó este enfoque para mejorar la calidad y eliminar barreras a la producción eficiente. Inicialmente se implementó en la industria automotriz, pero hoy en día se ha expandido a una amplia variedad de sectores, empresas y áreas de trabajo, ya que ha demostrado ser altamente efectiva en diversas industrias, optimizando la eficiencia, mejorando la calidad y reduciendo costos.
Dentro de Lean Manufacturing, existe una sub-metodología conocida como 5S, que se centra en la organización del lugar de trabajo.
El primer paso consiste en realizar un diagnóstico de la situación actual de las áreas de trabajo. Para ello, se lleva a cabo un análisis detallado de los procesos productivos, espacios de trabajo y condiciones en las que se encuentra el ambiente laboral.
Este diagnóstico ayuda a identificar las áreas de mejora, así como los principales problemas relacionados con el desorden, la acumulación de materiales innecesarios y la falta de estandarización en ciertos procesos.
Para ello se involucra a todo el personal en el proceso mediante la organización de sesiones de capacitación sobre las 5S y su importancia en la mejora de la productividad y la seguridad.
Proceso de implementación de las 5S
La implementación de las 5S no es un proceso rápido, ya que requiere tiempo, planificación y un cambio en la mentalidad de toda la organización. La metodología abarca las siguientes fases:
1. Fase de clasificación (Seiri)
Durante esta fase, los equipos de trabajo son instruidos para identificar y separar lo que realmente es necesario para su trabajo de lo que no lo es. El resultado de esto es la eliminación de una cantidad significativa de materiales obsoletos, herramientas defectuosas y otros objetos que ocupan espacio innecesariamente.
También se procura identificar qué herramientas y materiales se utilizan con mayor frecuencia, para asegurarnos de que estén siempre accesibles.
2. Fase de orden (Seiton)
El propósito de esta fase consiste en organizar las áreas de trabajo de manera que las herramientas y materiales estén en el lugar adecuado, etiquetados y de fácil acceso. Esta fase permite crear un entorno de trabajo más eficiente, donde todo el equipo sabe exactamente dónde encontrar lo que necesita sin perder tiempo buscando.
3. Fase de limpieza (Seiso)
Más allá de simplemente limpiar las áreas de trabajo, esta fase trata de que los trabajadores asuman la responsabilidad de mantener sus espacios siempre en óptimas condiciones. Esto no solo mejora la apariencia de las áreas de trabajo, sino que también reduce los riesgos de accidentes laborales y aumenta la motivación del equipo al trabajar en un entorno limpio y organizado.
4. Estandarización (Seiketsu)
Una vez que las fases anteriores: clasificación, orden y limpieza se han completado, el siguiente paso se encarga del desarrollo de procedimientos estándar, que deben ser seguidos por todos los trabajadores para mantener los niveles alcanzados en las etapas anteriores.
Para ello se implementan listas de verificación, auditorías periódicas y reuniones de seguimiento para asegurar que la estandarización se mantenga a largo plazo.
5. Disciplina (Shitsuke)
La clave de esta metodología es la constancia y el compromiso de todos los involucrados y para mantener la efectividad de las 5S a lo largo del tiempo, es esencial que toda la organización adopte una mentalidad de mejora contínua.
En esta etapa, es fundamental que los hábitos aprendidos se conviertan en una segunda naturaleza para los empleados, lo cual sólo puede ser posible si se establece una supervisión regular, acompañada de una creación de cultura de responsabilidad, para conseguir que las mejoras implementadas perduren en el tiempo.
Resultados del proyecto hasta la fecha
El fin de este método es crear un entorno de trabajo organizado y productivo, que promueva el bienestar de los empleados, consiguiendo mejorar la calidad del servicio ofrecido.
El proceso trae consigo múltiples beneficios que se pueden comenzar a reflejar en diversos aspectos de la empresa:
- Mejora de la eficiencia y productividad: La eliminación de desperdicios y la optimización de los espacios de trabajo han reducido significativamente los tiempos improductivos, permitiendo que los empleados se concentren en actividades de mayor valor.
- Reducción de riesgos laborales: El mantenimiento de un entorno de trabajo más ordenado y limpio, produce que el número de accidentes y riesgos laborales se vean reducidos.
- Mejora en la motivación y satisfacción laboral: el compromiso de los empleados, consigue crear en los mismos un sentimiento de seguridad en su entorno laboral, ya que en parte la organización es gracias a ellos, lo que hace que el ambiente laboral mejore.
La implementación del método Lean Manufacturing, y por tanto de las 5s en la empresa, así como en cualquier entorno laboral es un desafío, pero también una oportunidad para llevar a cabo un negocio más eficiente, seguro y orientado al futuro.
Comparte esto
También te puede interesar
Estas publicaciones relacionadas
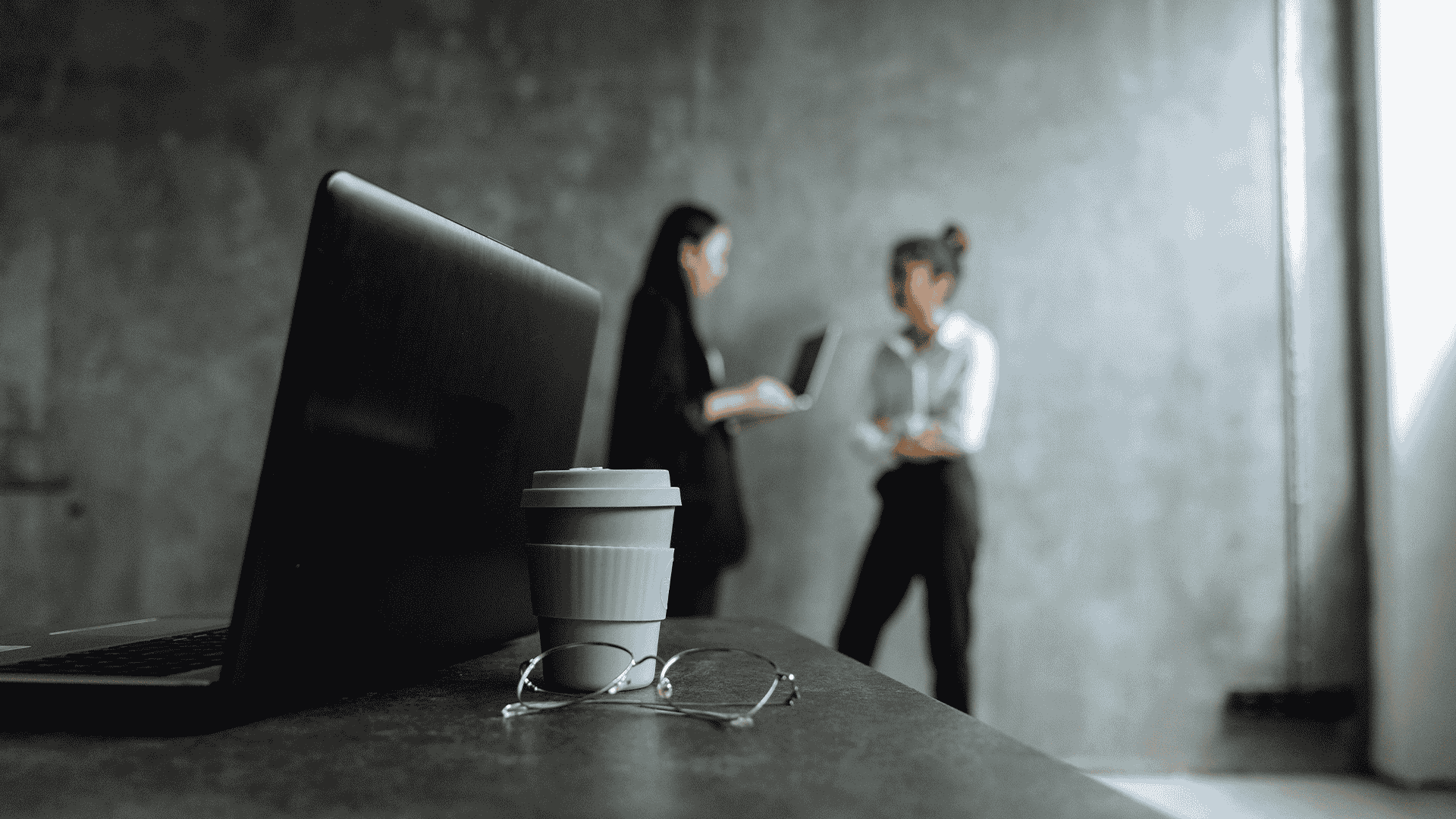
Kick-off Monday: Un impulso a la comunicación
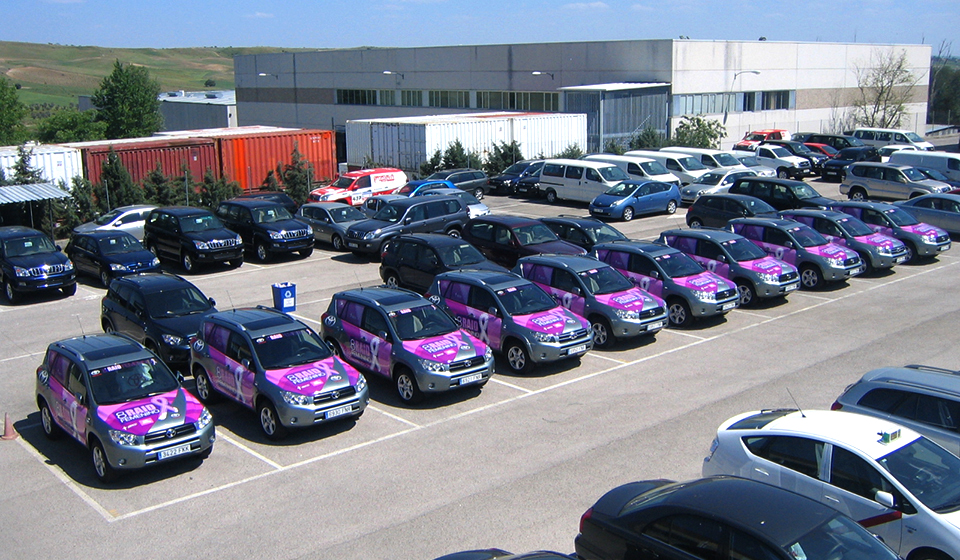
Vinilado corporativo de alta calidad: La clave del éxito en la publicidad móvil
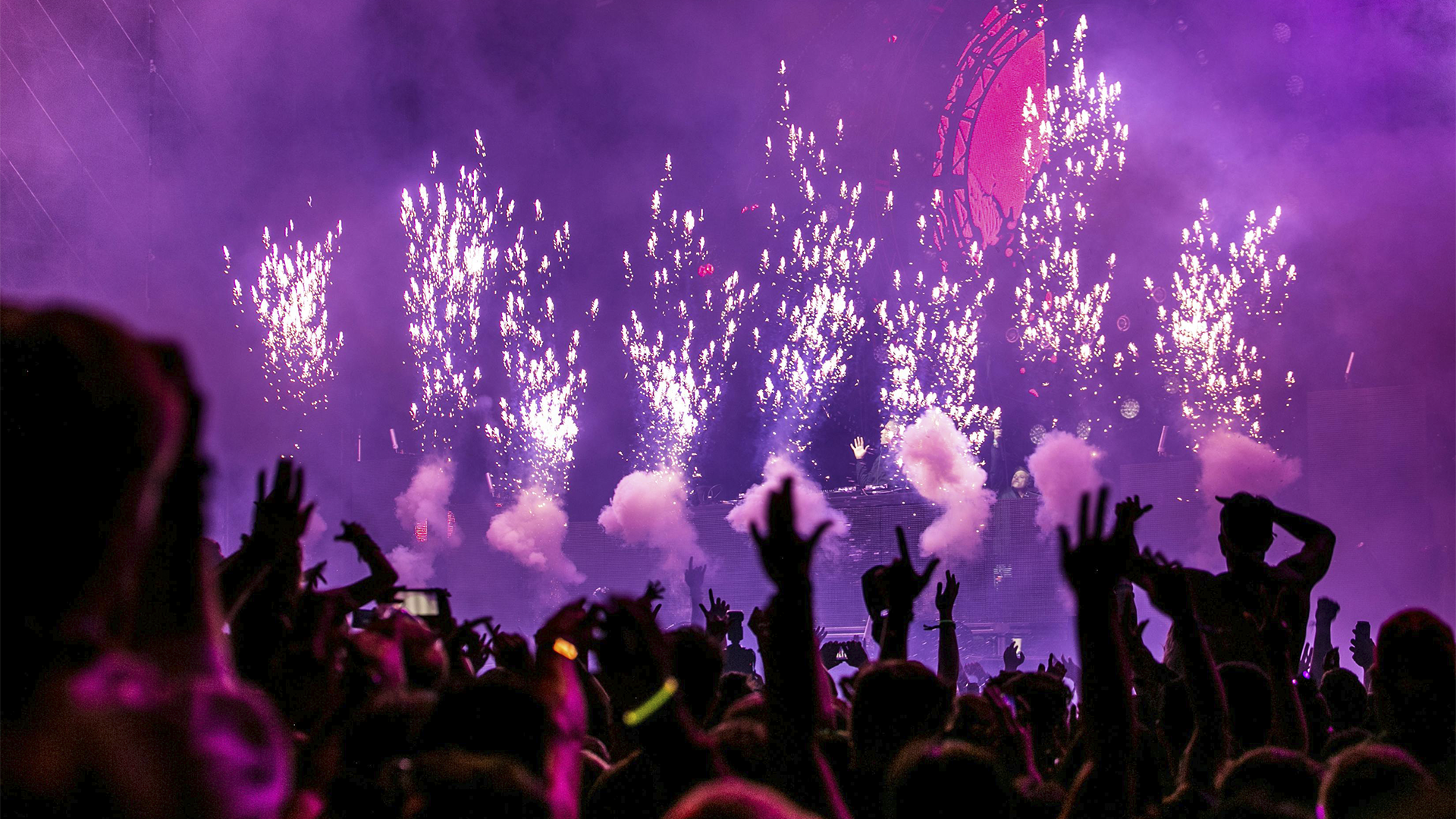